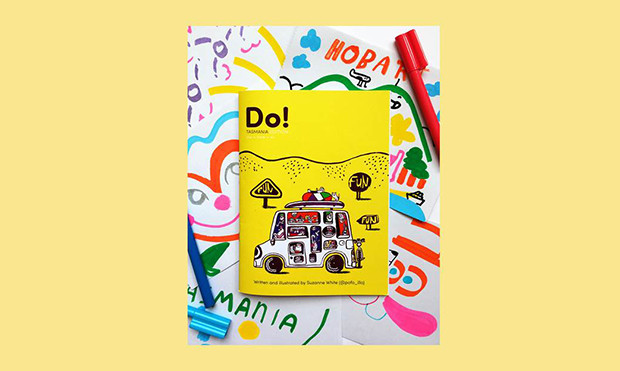
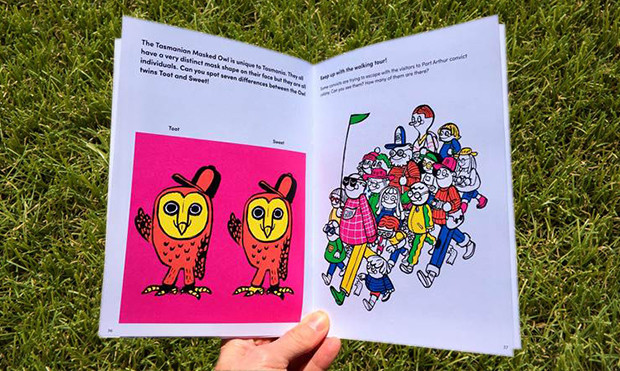
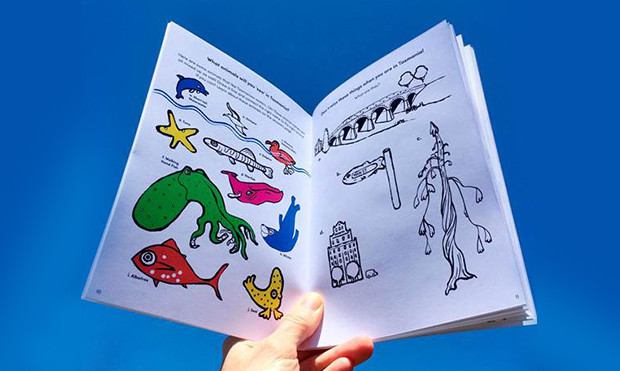
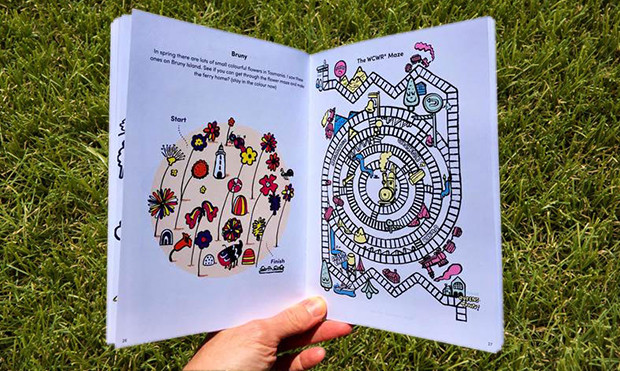
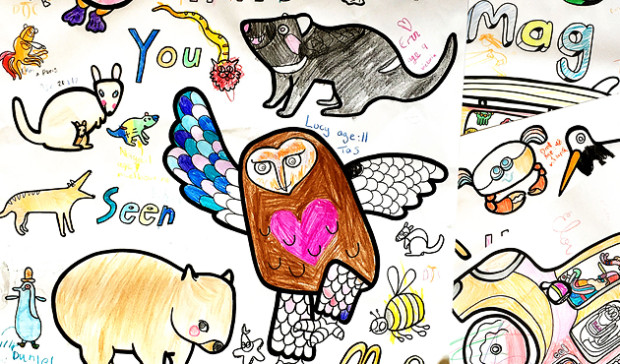
The final issue of BJ Ball New Zealand’s GSM covers a great story about the making of our brand. Designed by Sydney agency For The People, the task was not an easy one! Merging two prominent companies in the same industry and creating a new story, was a big task.
———————-
Mid-2017, two of the largest commercial print supply merchants in Australia merged; K.W. Doggett and BJ Ball—became Ball & Doggett. The merging of these two industry heavyweights was always going to present significant opportunities. One such opportunity was brand.
Historically, both entities have had their own stories to tell and legacies on which to draw. K.W. Doggett takes its name from the Doggett family who founded the company in the late 1960s. BJ Ball has been supplying paper in New Zealand for nearly 100 years, before moving into the Australian market in recent decades. But as the saying goes, ‘the past is the past, the future belongs to now’. And that future is Ball & Doggett.
GSM caught up with Jason Little, Creative Director and co-founder of Sydney-based For The People, AGDA Studio of the Year (2016)—to talk about paper, brand and everyone being on the same page.
GSM: How did you come to work with Ball & Doggett on the project?
JL: Getting to work on a project like this was quite fortuitous, but it’s equally an outcome of good relationships over time. Working in Australia since 2002, I’ve had my fair share
of print projects, and over those years developed some good working relationships with some lovely and helpful people at BJ Ball. During my stint as AGDA NSW Chairman a few years back, I began working even more closely with BJ Ball to support their needs as a sponsor. When I began For The People, Tony Bertrand at BJ Ball was very supportive, and gave us one of our first projects—The Mohawk Show.The relationship has been stronger ever since. After a proposal submission, discussions with representatives from both companies—Catherine Doggett & Tony Bertrand, we received the job.
GSM: Run us through the thought process behind the project.
JL: Working in print has changed. The traditional paper industry has had to shift its thinking, and start looking at new avenues for growth. BJ Ball & KW Doggett know this, and have been working hard to adapt to the ever-changing needs of customers, staff, and the industry itself. In mid 2017 they joined forces as part of a merger to form the largest commercial print supply company in the Australian market, Ball & Doggett. This was big news and a big change for the Australian industry, which was essentially bringing two of the three largest players together. When the brief for this project arrived, there was an obvious enthusiasm from the studio. We assembled the team: Amanda, James, Liv, Damian, Sunil, Ed and myself. We worked through a rapid immersion in the businesses, research and intensive engagement with the people of both companies, the products, and a diverse array of clients and customers. A vast amount of interviews, site visits with impromptu conversations and desk research allowed us to really observe the strengths, cultures and ambitions of both businesses. From here we were able to formulate some hypotheses about the newly merged company and where it could potentially position itself.The final objective of this project was to build a brand for the newly named Ball & Doggett (the name was also part of the process), that was not only true to the two businesses and the people, but also one that sets a bold vision for its future. We needed to present back a strong point of view on what that vision could be; how the new direction could consolidate their ambitions and help them drive the business forward, whilst connecting with its highly diversified clients.
GSM: How did you come up with the new Ball & Doggett identity? What is it about?
JL: The merger was as an opportunity to build a new identity that better reflected the true nature of the business—that of a highlydiversified, innovative company that supplies every material associated with the print and production supply chain. It needed to move beyond the perception of a paper merchant stuck in the past, and really start to show how the company fits into the digital ecosystem of today. The diverse set of customers meant that the identity needed to flex in tone whist maintaining a coherent story.We were very conscious of trying to show the company’s knowledge, passion and enthusiasm for their products and the relationships they’ve built with clients.
Testing paper weight, mixing ink and polishing foil were some we put through the lens of Willy Wonka and the materials factory, where thingsare never ordinary. And so the brand began to take shape from there.
The simplified letterforms of the brandmark enable it to demonstrate various behaviours and material properties. This was coupled with the imagined weird and wonderful manufacturing processes to show the joy in all materials. When it came to anything printed, materials are pushed to the front in applications. This meant toning down or straight up avoiding excessive graphics, and instead leaning more towards utility of information, simplified typography and a focus on making the materials do all the talking. The material is the central piece—its colour, texture, smell, weight, and so on, and every piece of design is there to support it, not distract from it.Understanding the need to tell a human story, we also worked with illustrator Deborah Ho to create a series of character illustrations to reflect the people of Ball & Doggett. These are then used for navigation and informative elements online, and across internal communications to facilitate the merger transition.
GSM: You worked in a highly collaborative and transparent way with Ball & Doggett—can you elaborate on this approach?
JL: We’ve been working in a completely open and transparent partnership with clients since we began the studio three years ago. It has meant that there are little, or no, secrets. From the start, we really try to immerse ourselves in the project, and the client’s business, whilst intensively engaging with the client team. From there, everything is shared and communicated almost daily. We really throw ourselves head first, and look to work through a shared commitment and authorship.
There is a constant conversation: thoughts and progress are shared through Slack, lo-fi videos of internal discussion and developments are recorded and uploaded, there are regular phone and Skype chats, there are face-to-face meetings
to share the larger milestones of the project with a wider group. Essentially, the evolving process of our thinking is seen, shared and discussed throughout the process.
One particular instance of this was for a critical meeting to share our creative concept. It involved the team standing around a wall in our studio, iPhone in hand, with Catherine Doggett on Skype, at the other end. The video discussion bounced around from talking to the screen, to pointing the phone at stuff on the walls, moving in closer to show specific details or information, and then back to me or a member of the team. It was presenting the main creative idea in its early and imperfect iteration. However, it was building on prior ad-hoc conversations we’d been having, so was less of a ta-da moment and more of a thought share. This kind of loose chat is typical. It’s not for everybody, but for most of our clients it works. There is no pretence or formality once the project gets going. We’re all in it together trying to find the best outcome, and it makes the process far more enjoyable.
GSM: What challenges did you face while working on the project?
JL: This is an enviable project to work on—ensuring it delivers on the needs of the organisation and its people, whilst delivering a good creative result, is probably the main one.There were obvious concerns about a potential convoluted decision-making process, but this never materialised—it was a very straightforward process, we were working closely with the decision makers, and consensus was easily achieved on the work. We hit a brick wall for a period during the design sprint, where we had some issues in crafting the identity so that it could showcase the material properties. We finally cracked it once we brought a level of simplicity to the logo. This allowed us to go further in execution through the 2D and 3D work.
GSM: Where is the identity at and what’s next?
JL: The brand is still very new to the market. We’ve developed the core parts of the identity and developed the design intent for a number of areas. We’ve created 3D illustrations and animations with some cracking animators, Dominik Grejc and Georgiy Kuznetsov, for use online and in marketing publications. Various pieces of print and digital communications are being worked on by the B&D team, The Company You Keep, and ourselves. We’ll be looking to build out and shoot some of the material testing experiments when the opportunity presents itself further down the track.As Ball & Doggett look to the future, this new brand gives them the flexibility to adapt and develop in untapped markets, create new tools for their customers, and stay relevant as the market changes. I’d anticipate further collaborations, with great designers and studios, to interpret the branding and help it live up to the ambitions I have for it.
GSM would just like to clarify for our Kiwi readers that Ball & Doggett is the Australian entity for BJ Ball. In New Zealand the company remains known as BJ Ball. Thanks.
We recently released an A5 sampler created by A Friend of Mine design studio in Melbourne, consists of a set of seven cards (read more about it in the previous post). One of the cards, printed on a Dry Toner machine, is what we’re going to share our knowledge about today.
Designer: A Friend of Mine. Photography: Sarah Anderson.
In print land, there are many ways you can print an image. Dry Toner print means laser printer and is a great choice for short run work. Dry toner machines are the most common print machines out there so you can often get work done quickly and at a competitive price. Like all digital printing there is very little set up (no plates) meaning each impression can be different to the next, think personalisation and the ability to mix up the colours on the same job.
Dry Toner printing has made leaps and bounds in terms of print quality and enhancement too, now offering a broader gamut of colour via CMYK but also clear, silver and gold toner options too. Dry toner is really up there for quality now and we actually think dry toner silver gives the best metallic print result you can find but shhh don’t tell the offset guys!
Economical embellishment with clear toner
The idea of this piece was to show you can mimic spot varnish with the use of clear toner. It’s a really economical trick and great for when you only need a small amount of business cards or an invite. On first glance of the printer’s proof we immediately saw the clear ink was too subtle on the bright pink. We wanted more impact so decide to put 30% magenta down first and then print the clear toner over the top. This gave greater contrast between paper and print. And by putting the clear toner on last it gave a nice shiny finish, mimicking the look of an expensive varnish.
TIP: the more matt and rough the paper is the greater contrast with the shiny clear toner. This trick works beautifully on dark papers and can be mistaken for a clear foil. Much cheaper and quicker than getting a foil block made and ideal for those times when you need some quick impact.
Looking for some additional inspo? Here’s some dry toner tricks just for you:
1. Clear ink on black stock to create a shiny, rich black effect.
2. Clear ink on white stock can achieve a subtle, modern white foil effect
3. Print a clear ink pattern over black text for a textured print effect
4. Dry Toner Silver and Golds come in all shades from yellow gold through to cooper, pewter and flat silver. It’s a mix of silver and yellow and the shades are endless.
5. Want a thick card? We sell cardboard that can be printed and stuck together under pressure. Mulitloft and Mohawk layers are the two products. It’s a cheap way to get super lux thick business cards on a short run, quick turnaround basis.
If you ever have any production questions, speak to your business development executive or call our marketing department on either 02 8863 1266 or 03 8794 3407.
Spec:
Dry Toner on Pop’Set Cosmo Pink 320gsm.
Printed: 30% Magenta plus clear toner on front. Silver toner on reverse.
A5 cut short grain.
We recently released an A5 sampler created by A Friend of Mine (AFOM) design studio in Melbourne, consisting of a set of seven cards wrapped in an origami folded B2 sheet. And we folded them all in-house. We owe a lot of people a big thanks for their help! Inspired by the shape formations found in paper, each card in the sampler showcases a variety of digital print techniques and a custom perforated shape. It’s been a doozy of a production project but worth it.
We wanted to share some important printing hints and tips around the Curious Collection Skin Red 270gsm card. The red card was printed on a HP Indigo press using CMYK, white AND fluoro pink ink. The checked pattern looks simple enough but delve deeper and there’s quite and few tricks we implemented to really make it pop. We did the hard yards so you don’t have to.
Designer: A Friend of Mine. Photography: Sarah Anderson.
What we learned
The artwork file is made up of seven layers. Getting the order of ink lay down is imperative. To get the tonal effect between the opaque and translucent areas of ink, the white gets laid down first, 3 hits to be exact. Then we follow up straight away (electro ink dries instantly) with the CMYK. On this piece CMYK shows up as the green, navy blue, magenta and maroon layers. To ensure they sit over the white, all CMYK areas need to be set to OVERPRINT. For a further explanation of what overprinting is click here. The ink that hits the white becomes opaque and has a bolded look. Ink printed directly onto the paper looks more transparent and subtly shows the stock colour underneath. Finally, the fluoro pink ink is laid down. Fluoro ink has a translucency so when it hits the white ink it pops as pink but when it hits the red stock it makes a slightly darker red shade.
Important to also mention that printer’s proofs are essential, especially when working with white ink. We went a few rounds with these before getting it right and consulted the printer regularly to achieve the desired result. Look out for registration too, with so many layers it’s important the edges of the pattern all line up. Finally there is a lot of ink coverage on this card, however AFOM has been mindful to keep some areas of the paper ink-free for all the paper lovers out there who want to feel Curious Collection Skin’s silky tactile goodness.
If you ever have any production questions, speak to your business development executive or call our marketing department on either 02 8863 1266 or 03 8794 3407.
Spec:
• Curious Collection Skin i-Tone Red 270gsm
• Printed HP Indigo
• Duplexed (1 sheet short grain, 1 sheet long grain- this minimises the curling that can happen with duplexing)
• CMYK, white ink (3 hits) and fluoro pink ink
In 2016, we got to be a part of something pretty spesh when it comes to the world of paper and print. The culmination was the limited edition book The Sub Divide. It’s part print, part art and a whole lot of beauty. A curated resource celebrating a selection of 30 highly regarded photographers – recommended by and for, the creative industry. The publication has been developed by a collective of specialists dedicated to their craft.
(Most of the content from this blog post first appeared in Issue 11 of GSM Magazine).
The Sub Divide is an exquisite printed resource developed through the pillars of inspiration, experimentation, collaboration and celebration. It also celebrates craftsmanship. With a unique collaborative approach to production, this resource came to life through the dedication and expertise of some very committed individuals. The project started with a simple conversation between John Wanless Director at Bambra Press and one of staff after they saw printed test sheets of photographic material lying on Bambra’s press room floor. Grosz Co. Lab’s Creative Directors, Ben Grosz and Laura Camilleri then became involved by developing the concept and curating the collection of photographic works which the book showcases. Their efforts were none other than extraordinary!
The collective behind this project comprised includes:
> Bambra Press for Initial concept and delivering exceptional print.
> Grosz Co. Lab for the development and curation of the publication through intelligent, articulated design.
> Huber Inks for the supply of the Pacifica Inks and also specialist guidance on technical advice during the process, supplied by Ball & Doggett.
> The Bindery for the development and production of the unique featured binding techniques.
> Avon Graphics for the production and expertise in embellishments and foiling.
> Foldercorp for the production of the sleeve.
> Cartonlux for laminating the stock for the sleeve.
> Nordale Graphics/Wibelin for the binding techniques.
And yours truly for the supply of paper (visit our existing websites until the Ball & Doggett one is live).
Such a complex print project presents many technical challenges. A key driver to the success of the publication was the extensive research and development phase. This included a series of mock-ups created by our Designline team in VIC that enabled dialogue with everyone involved. Creating a mock-up although it doesn’t have any print is a key step in any major print project and can save a lot of time and ensure the end product is exactly what you want.
One of the specific technical challenges presented, was the unique bind which creates both an interesting aesthetic experience and is also unusual in placing the index containing the details of the featured photographers in the middle of the book. The bind solution was developed by Ian Leckie, operations manager at The Bindery.
The slipcase (1) uses Colorplan Cool Grey 270gsm stock which has been custom diecut, folded and hand-glued, then duplex laminated to Colorplan Pristine White 270gsm. The embellishment across the slipcase features foiling by Avon Graphics with an API Foil (2004 / CL Clear Rainbow).
The bind design (2 + 3) uses a unique concertina fold to connect the two sections of the book together. The cover uses 350gsm Colorplan Cool Grey stock, on which a range of tactile embellishments have been employed including a multi-level emboss using a hand-carved sculpted die on the front cover (3), and on the back cover (4) a blind press using a foil stamping die without the counter die.
The inside front and back cover (5 & 6) use an API Foil (2004 / CL Clear Rainbow), and the spines and concertina fold (7) employ a blind deboss and foil. The index (8) is cleverly positioned at the centre of the book to make maximum use of the extra real-estate allowed by the open concertina fold, and was foiled using a blue metallic foil.
> The internal text pages of The Sub Divide were printed by the team at Bambra Press in CMYK, using Pacifica Inks throughout, on a Heidelberg XL75 12P
+ Aqueous Coater using Fuji Film CTP Processless Plates. Various screen rulings (specifically developed by Bambra Press) were selected to ensure the best possible result across each section of the book.
After 15 months of development from concept to production, The Sub Divide was officially launched in October 2016. A testament to the quality of the finished product, Grosz Co. Lab were recipients of a gold medal in the Print/Design Category at the recent 34th Annual National Print Awards.
For a more information on the production methods used in the project visit www.thesubdivide.bjball.com.au
Please direct any queries about The Sub Divide to Zaidee Jackson, Business Development Manager via zaidee.jackson@ballanddoggett.com.au
The Sub Divide features the work of 30 highly regarded Australian photographers. Published together for the first time, the photographers responded to catergorisations divided into two groupings. The first, a commercial response to ‘people’, ‘place’ and ‘pieces’. And the second category was a response to ‘passion’, exploring the photographer’s personal connection, depicted through their lens.
> Amanda Austin //amandaaustin.net
> Andrew Curtis //andrewcurtis.com.au
> Anna Pogossova //annapogossova.com
> Ben Glezer //beng.com.au
> Ben King //benkingphotographer.com
> Bonnie Savage //bonniesavage.com
> Brooke Holm //brookeholm.com.au
> Cecille David //cecilledavid.com
> Christian Blanchard //christianblanchard.com
> David Rosendale //davidrosendale.com
> Derek Swalwell //derekswalwell.com
> Dieu Tan //dieutan.com
> Eve Wilson //vevewilson.com.au
> Foliolio //foliol.io
> Fraser Marsden //frasermarsden.com
> Heather Dinas //heatherdinas.com
> Ingvar Kenne //ingvarkenne.com
> Isamu Sawa //isamusawa.com.au
> James Geer //jamesgeer.com
> Jamie Macfadyen //jamiemacfadyen.com
> Jeremy Blincoe //jeremyblincoe.com
> Justin Ridler //justinridler.net
> Lynton Crabb //crabb.com.au
> Mark Lobo //marklobo.com.au
> Peter Bennetts //peterbennetts.com
> Peter Greig //petergreig.com
> Shannon Mcgrath //shannonmcgrath.com
> Tim Jones //timjones.co
> Toby Scott //tobyscott.com.au
> Zoe Economides //zoeeconomides.com
This article was originally published in GSM Magazine, created by BJ Ball New Zealand.
MultiLoft™ Encore is made using Convertible Solutions cohesive glue technology and Mohawk’s Superfine range of papers, certified to run on the HP Indigo press.
Looking for a pimped-up business card, with comps, wedding invite or greeting card that takes thickness to the max? MultiLoft™ Encore is where it’s at. Colour is built into the sheet of paper. So it’s ultra white on one side and coloured on the other side. And we also sell insert colours so the options are endless.
To achieve double the thickness of what is an already pretty thick card, print on the white side of two different sheets of MultiLoft™ Encore and then stick them together. Each double thick finished piece is approximately 634gsm.
The MultiLoft™ Encore inserts have cohesives (sticky stuff) on both sides and can be placed between the sheets to create colourful, eye-catching projects. As an example, adding x1 insert sheet, the thickness goes up to approximately 904gsm. Keep adding inserts to achieve your desired thickness.
After your project is printed and constructed, you can then diecut your job into the desired shape.
The range
MultiLoft™ Encore sheet colours: Ultra white/Kraft (brown), Ultra white/Black Licorice, Ultra white/Wild Cherry, Ultra white/Pacific Breeze, Ultra white/Orange Fizz, Ultra white/Blue Raspberry. Click here for the full sheets stock chart.
MultiLoft™ Encore insert colours: Kraft (brown), Black Licorice, Wild Cherry, Pacific Breeze, Orange Fizz, Blue Raspberry.
We love this marketing suite for OPUS on Hutt Apartments. Designed by Black Sheep Advertising in Adelaide for their client Proton Developments, the brochure emanates quality attention to detail and the business cards are just class.
OPUS (which means masterpiece), is a premium apartment development in the Adelaide CBD offering larger than usual apartments. Most places currently on the property market are substantially smaller in comparison. Plus, OPUS boasts all the dreamy bells and whistles like innovative integrated technology, premium finishings and fittings and a modern layout. Yes, we want to move in too. Get in line!
Creating a printed piece that stands out from the crowd is no mean feat. It practically has to yell your name and buy you a coffee to get your attention. Black Sheep Advertising have designed a clever marketing suite that is next level and reflects OPUS’s unique inner city living offering.
The burst bound brochure, printed on Knight Smooth, is over-sized and has a deliberate coffee table book feel. Black Sheep Advertising shares: “It was important to have print as part of our execution. Firstly, a functional reason – when people are looking to buy into a development it is important to be able to provide them with something to take home and return to multiple times.” The brochure’s dust jacket is treated with an all over soft touch Plasticoate laminate (it literally feels like it sounds) and a swish copper foil for the logo to add extra wow. The textures and colours throughout the brochure pick up on the architectural colour palette of the build.
The stationery and business cards are also printed on Knight Smooth. Again, the soft touch Plasticoate laminate and copper foil feature on the business card. Black Sheep mentioned to us: “When you hold the business card or the brochure in your hand, you can tell the project is one of quality and that sense is left with you after you put it down again.”
Find out more about the project which seeks to provide a quality of apartment living never seen in Adelaide before at www.opusonhutt.com.au.
Brochure:
24pp + 4pp cover
Finished size: 416 x 306mm
Cover: PMS 425 (Grey) + Black + o/all matt sealer varnish (outer) + PMS 425 (Grey) + PMS 876 (metallic) + Black + o/all matt sealer varnish (inner)
Text: CMYK + o/all matt sealer varnish t/out
Dust jacket: PMS 425 Grey + Black + soft touch cello + copper foil / matt sealer varnish to inner
Stock: Cover: Knight Smooth 350gsm, Text: Knight Smooth 170gsm, Dust Jacket: 140gsm Knight Smooth
Business cards:
Finished size: 90 x 55mm
Front: Black + PMS 425 (Grey) + PMS 876 + metallic copper foil + soft touch cello
Back: Black + o/all matt sealer varnish
All four corners forme-cut round
Stock: Knight Smooth White 400gsm
Letterhead and with comps:
Letterhead finished size: 210 x 297mm
With comps finished size: 100 x 210mm
Front: Black + PMS 876 + o/all matt sealer varnish
Back: PMS 876
All four corners forme-cut round
Stock: Knight Smooth White 120gsm
We all love a bit of bling on paper, especially the gold variety, or silver, or bronze…we’re not fussy! Matt Murcott, Director at Matte Gold sure knows how to make paper sparkle. Being in the business of embellishments, they specialise in foil stamping, embossing, forme cutting, holographics and even highly secure hologram foils.
Family owned and operated, Matt first sighted a foil-stamping machine as a child in the Moorabbin factory where his father worked. After countless school holidays cutting his printing teeth on the Milford Astor hand foil stamping press, at 17 years of age, Matt began his foilstamping apprenticeship. The rest is history. Matt shares: “Matte Gold was always going to be realised – it was just a matter of when…”
Now a Foilmaster in his own right, Matt and his team work on some seriously cool projects from shimmering candle labels to stickers for tattooists, specialised business cards with coloured foils and specialty applications like Perspex and leather. For the last five years Murcott has worked closely with the RMIT Design Management and students, sharing his knowledge of the trade and is also on their Program Advisory Committee.
The embellishment industry has come a long way in recent years and business is constant for Matte Gold. The biggest challenge has always been about education, for designers and consumers. Matt says: “Offshore options for consumers are slowly being reigned in thanks to poor quality and slow turnarounds but what remains is the ‘I want it now and I want it cheap’ issue… Designers are more inclined to ask questions before pushing the boundaries.”
When asked what the ultimate job would be, Matt said: “We do a bit of work with musicians and tried to get a spot producing some items for Midnight Oil’s tour this year, this would have been my personal dream project if we had pulled it off. Other than this, a lot of our work is so much fun and some days what we are doing right now, is dreamy enough.”
You can check out more of Matte Gold’s flashy creations here.
Project name: Planned Parenthood mural
Partner-in-Charge/Designer: Paula Scher
Associate Designer: Courtney Gooch
Project Manager: Sarah McKeen
Photos: Peter Mauss/Esto
We spotted this excellent example of wide format (commonly known as outdoor media), on the Pentagram blog. What we love about this project is the use of a not often spoken about product that we stock – wide format media eg billboards, point of sale, window and floor graphics, banner vinyls, light boxes and indoor/outdoor advertising. A big thanks to the Pentagram team for allowing us to post their story, a snapshot of which appears in the ‘Snippets’ section of our first edition of Spot. Speak to your paper specialist for a copy.
Planned Parenthood is America’s most trusted non profit provider of reproductive healthcare (an estimated one in five American women have chosen Planned Parenthood for healthcare at least once in her life and the organisation is currently powered b 9.5 million activists, supporters and donors nationwide). Paula Scher and her team designed a large-scale installation for the company’s new national headquarters in Lower Manhattan. The main mural goes up three staircases and was timed to coincide with the company’s centennial in October 2016.
Paula Scher and the team researched historic images, settling on about 30 in the end. They used a century of ephemera – a mix of newspaper ads, instructional posters from clinics, protest posters, pins, photos of protests, and other historical material (created by Planned Parenthood) for the mural.
To enhance image quality, they digitised them, then applied the Planned Parenthood colour palette (with the addition of bright yellow to tie in the environmental graphics into the existing brand identity). The design team worked closely with the architect and leadership team at Planned Parenthood to develop the installation. And other than the main installation, smaller murals appear on walls throughout large conference rooms and other meeting spaces.
As it states on the Pentagram blog: “The installation acknowledges the important role that activism and posters, placards, symbols and other graphics have played in garnering support. Many of the designs were originally created by grassroots activists, and the mural is a tribute to their impact in the movement for reproductive rights.”
To bring the mural to life, vinyl wall-covering built in layers for a dimensional effect, was installed. Acrylic forms were cut-out and mounted over the surface. The murals were a hit and now other Planned Parenthood offices want in on the action to. So do we Paula and the team, so do we. Fancy a trip to Australia??
If you’re one of our customers, visit the wide format section of our website for the products we carry that are similar to what Pentagram have used for the Planned Parenthood installation. If it all gets a bit much, call your paper specialist or account manager and they’ll be able to guide you in the right direction.